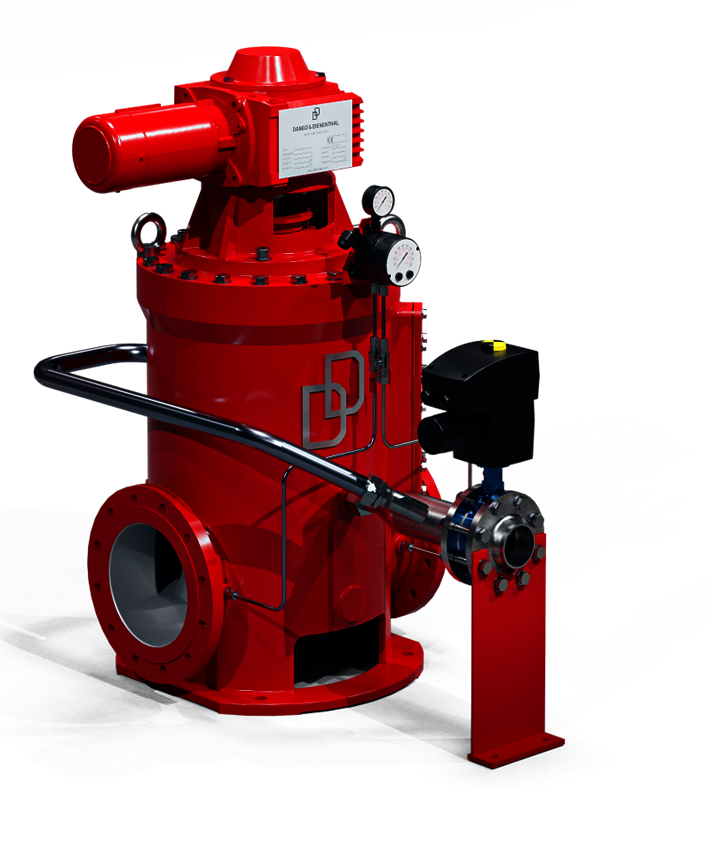
High-performance automatic filter for efficient fine and coarse filtration
Our Filterautomat was developed to optimize the filtration process while reducing the effort required for operation to a minimum. Thanks to its independent control and automated processes, the automatic filter is able to continuously monitor and adjust the filtration process to achieve optimum filtration results.
Its rotating filter drum ensures the uniform distribution and removal of solids over the entire filter surface. Its robust design and excellent backwash performance offers companies a reliable solution for the efficient filtration of solids for almost every industry. Contact our experts and find out more about our Filterautomat - an industrial water filter for solid-liquid separation.
Request product
Download brochure now
Our water filter for industries works independently and continuously, without manual intervention. It monitors the condition of the industrial filter and automatically adjusts the operating parameters. Solid-liquid filtration is not interrupted during automatic backwashing. There is no downtime for the entire water filter system.
Thanks to the constant filtration performance, you can increase your productivity by up to 20 %, avoid production interruptions and also ensure consistent operational reliability - even with changing dirt loads.
In addition, it prevents premature wear of sensitive system parts such as heat exchangers, fittings, flow meters or spray nozzles. This extends the service life of your system by 2 to 10 years and reduces unplanned downtimes by up to 25-35 %.
The level connections enable quick and easy installation - without having to relocate or adapt the pipes. Particularly with pipe diameters from 150 mm, you save on expensive commissions for installation companies. This reduces your planning and installation costs by 30-40 % and speeds up the commissioning of your system by up to 2 days.
Thanks to the already wired and tested unit, the time-consuming wiring and testing process is no longer necessary on site - the industrial water filter is ready for immediate use. This shortens your implementation time by up to 40 %, significantly reduces installation costs and minimizes potential sources of error.
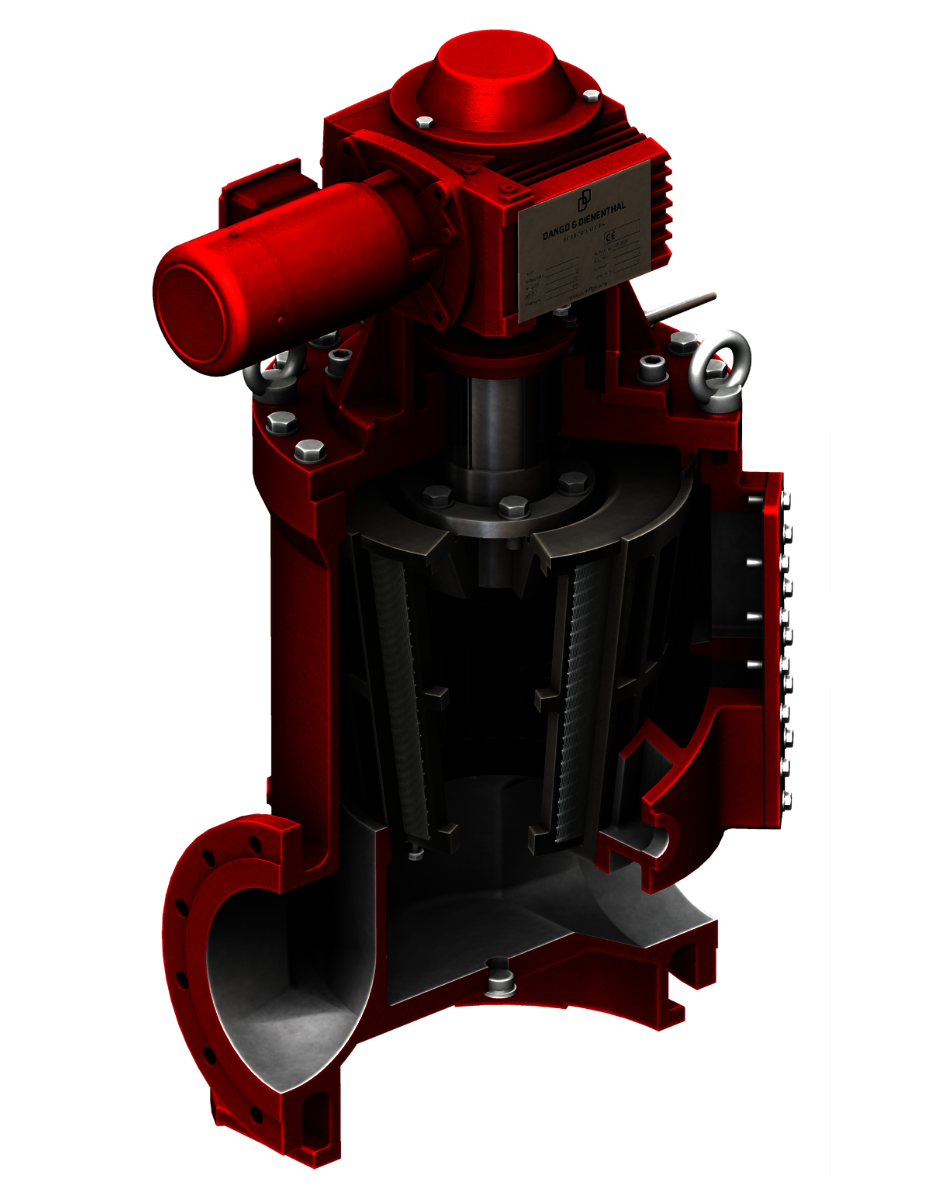
MAXIMUM CLEANING PERFORMANCE AND FINE FILTRATION DOWN TO 25 MICROMETERS
With cleaning speeds of 4 to 10 m/s and 100% cleaning of the entire filter surface, we ensure outstanding cleaning performance for every application. Even coarse particles are reliably sheared, while the fine filtration effortlessly traps particles from a size of 25 μm.
FLEXIBLE CUSTOMIZATION AND EASY INTEGRATION FOR VERSATILE FILTRATION REQUIREMENTS
Thanks to the uniform feeding of the entire filter surface and the option of integrating individual wedge-wire screens or wire mesh, the automatic filter offers a flexible and adaptable solution for every application. The compact inline design and fully pre-wired tested unit allows for quick installation and seamless integration into existing systems.
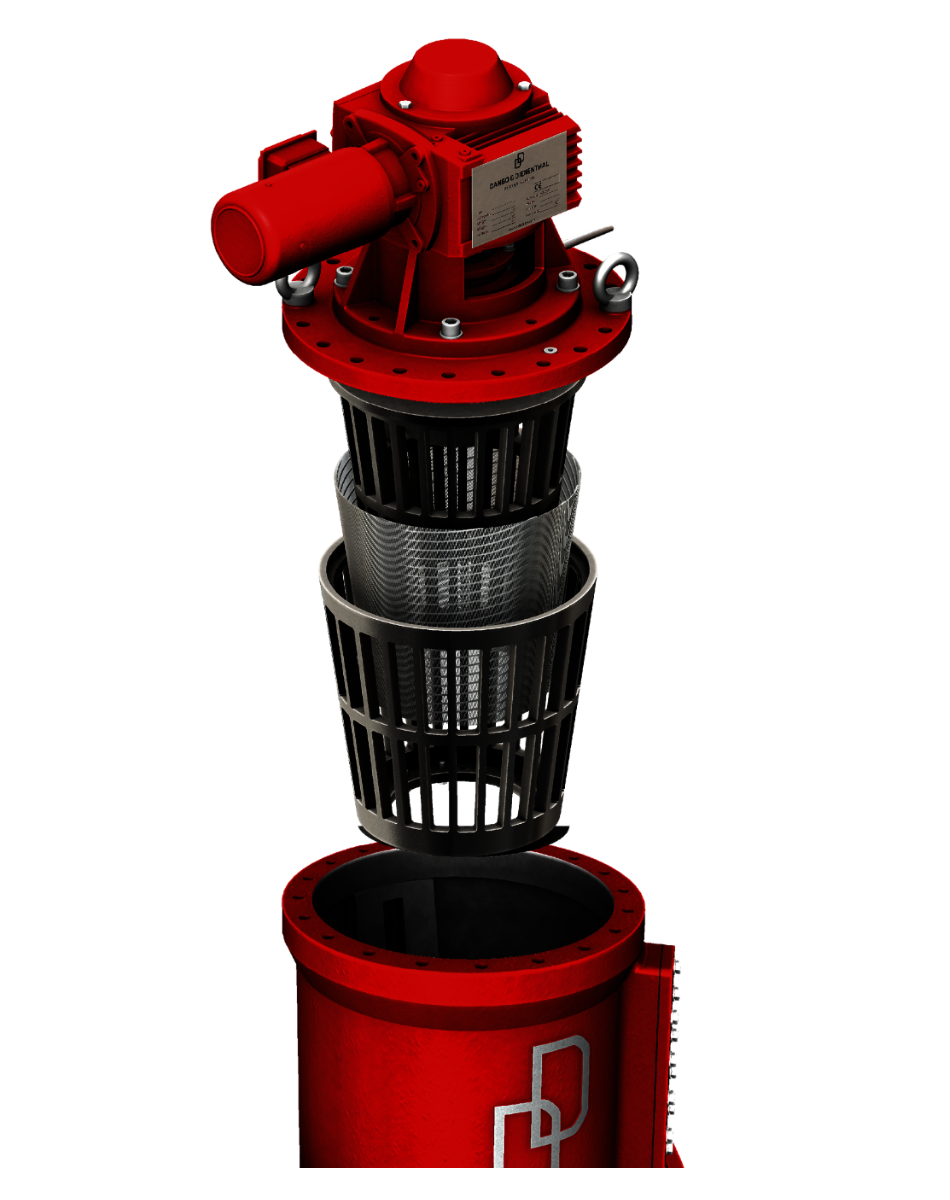

EFFECTIVE APPLICATIONS IN NUMEROUS INDUSTRIES
The automatic filter is versatile and can be used in industries such as steel, paper, chemicals and power plants. It also supports cleaning in wastewater treatment plants and the maintenance of building technology, while additionally ensuring clean systems in geothermal and offshore applications, the food industry, drinking water treatment and irrigation. Furthermore, it plays a valuable role in mussel control.
WHY A BACKWASH FUNCTION?
Backwashing is used to regularly clean the filter element to remove accumulated solids. This keeps the filter surface free and fully functional, allowing the filtration process to continue without interruption and with consistent efficiency.
HOW DOES THE BACKWASH FUNCTION WORK?
Automatic backwashing prevents blockages caused by deposits, which could otherwise result in increased differential pressure, reduced water flow and potential process disruptions. In this way, backwashing ensures constant cleaning performance extending the service life of the filter by removing contamination completely and in good time.
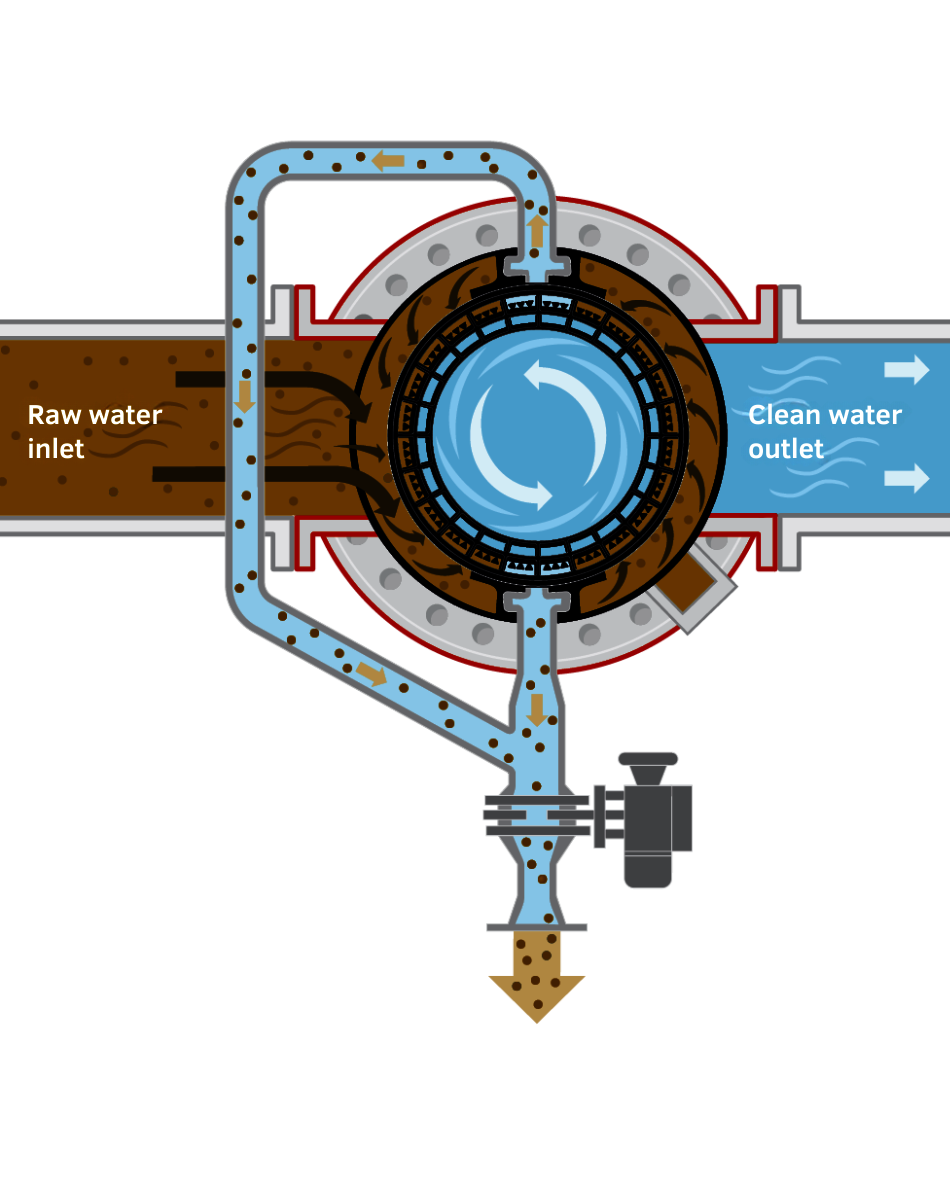
This video illustrates the individual steps of the filtration process.
From the entry of the raw water to the exit of the clean water, it shows the entire process and explains how the automatic backwash function works without interrupting the filtration process.
The motor-driven backwash valve opens, creating atmospheric pressure in the backwash line and in the flushing channels in the filter housing. Due to the excess pressure on the clean water side of the filter drum, the solids accumulated on the filter element are backwashed towards the atmosphere against the direction of filtration.
Filter housing
There are two opposite flushing channels in the filter housing. To prevent the raw water from entering the flushing channels during the backwash process, the flushing openings are sealed off all around with sealing surfaces. The filter housing is coated with a standard two-component epoxy resin coating. During assembly, the upper part of the filter is inserted into the filter housing, with the lower part of the filter drum centered in the filter housing by a ring surface.
The filter housing consists of a monolithic cast iron body with a silicate-based cast skin without weld seams - for particularly high strength and resistance to external and medium-based influences.
The result: a doubling of the service life of your filter system, a reduction in total operating costs of up to 30 % and halved disposal costs for old systems.
Filter drum
The filter drum consists of a sturdy, corrosion-protected support basket system with a conical design that holds the filter element in place precisely. Thanks to the conical design, the three individual parts can be fixed and screwed together with dimensional accuracy. Coarse particles are retained in the segment-like openings of the outer part and, if necessary, broken up between the filter drum outer part and the backwash channel. The special design with sharp edges between the filter drum and filter housing enables particularly effective fragmentation of coarse particles.
Thanks to the integrated shredding function, additional filtration stages are no longer required, eliminating the need for purchase and maintenance costs for additional input systems such as sieve belt systems or flotsam screens. This saves up to 600,000€ in operating costs over 20 years.
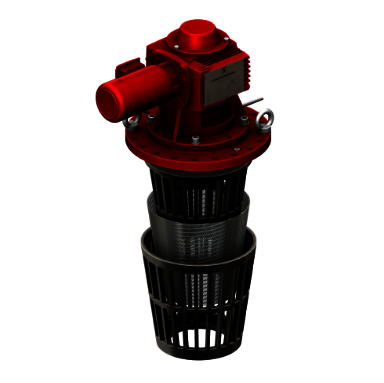
Filter element
With 100 % cleaning of the entire filter surface, the filter element ensures constantly low differential pressures. This significantly reduces the energy requirement of the pump - depending on the operating conditions and pump performance, you save 10-30 % of energy costs, reduce your operating costs and at the same time make an active contribution to sustainability.
Thanks to the easy option of switching between slotted screen and wire mesh, the filter element can be flexibly adapted to changing operating conditions and seasonal changes in the surface water within 1-5 hours.
This minimizes wear on important system components such as heat exchangers, fittings or spray nozzles, reliably protects your processes and enables long-term operating cost savings of up to 45 %.
Filter element: Wedge wire screen
The automatic filter can be equipped with different filter elements depending on the requirements. The wedge wire screen consists of welded stainless steel triangular rods and is characterized by an extremely robust design. It is available in various grades of stainless steel and offers a filter finenesses starting from 30 μm.
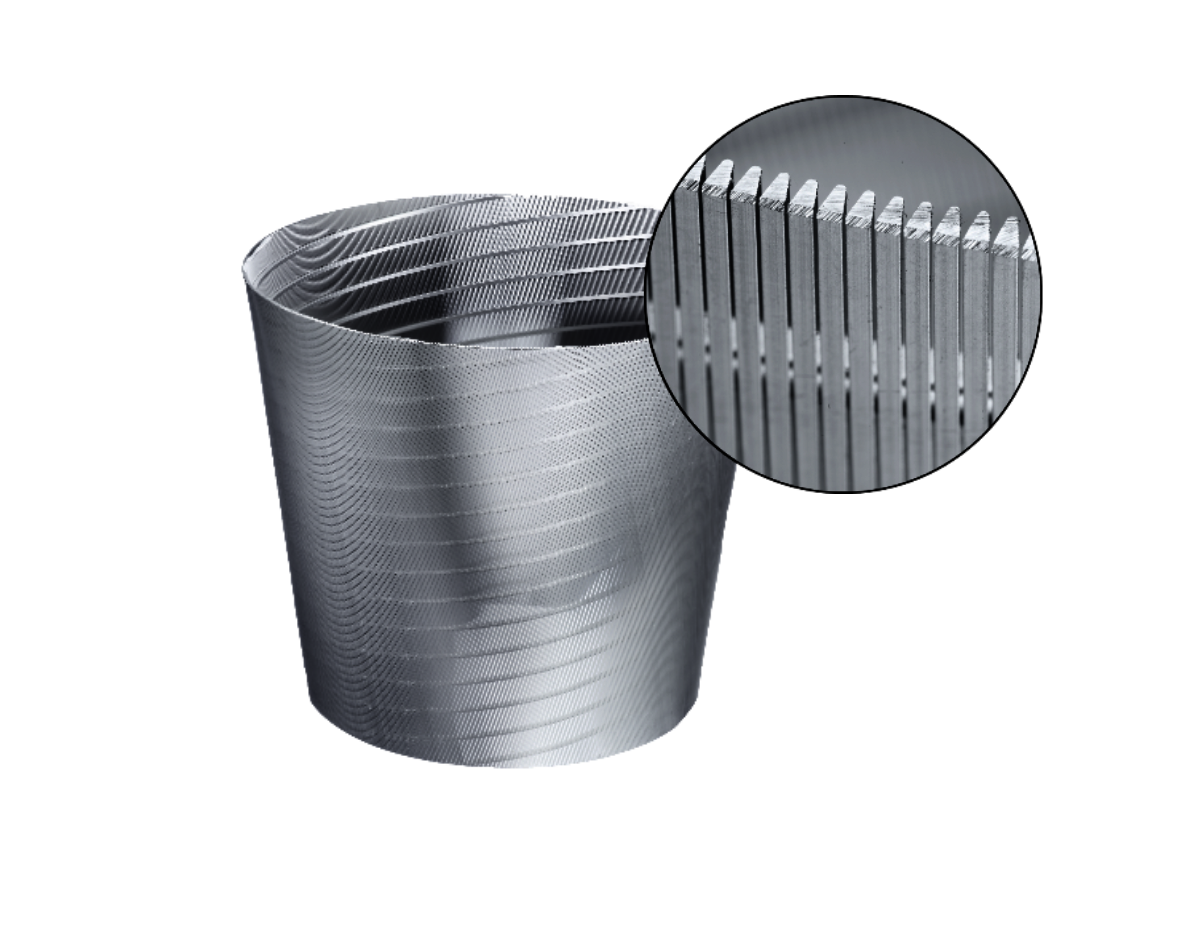
Filter element: Wire mesh
Alternatively, a wire mesh is available that is held in a sandwich construction by two supporting meshes, which enables a higher net filter area utilization. This element is also available in various stainless steel grades and offers a filter finenesses starting from 25 μm.
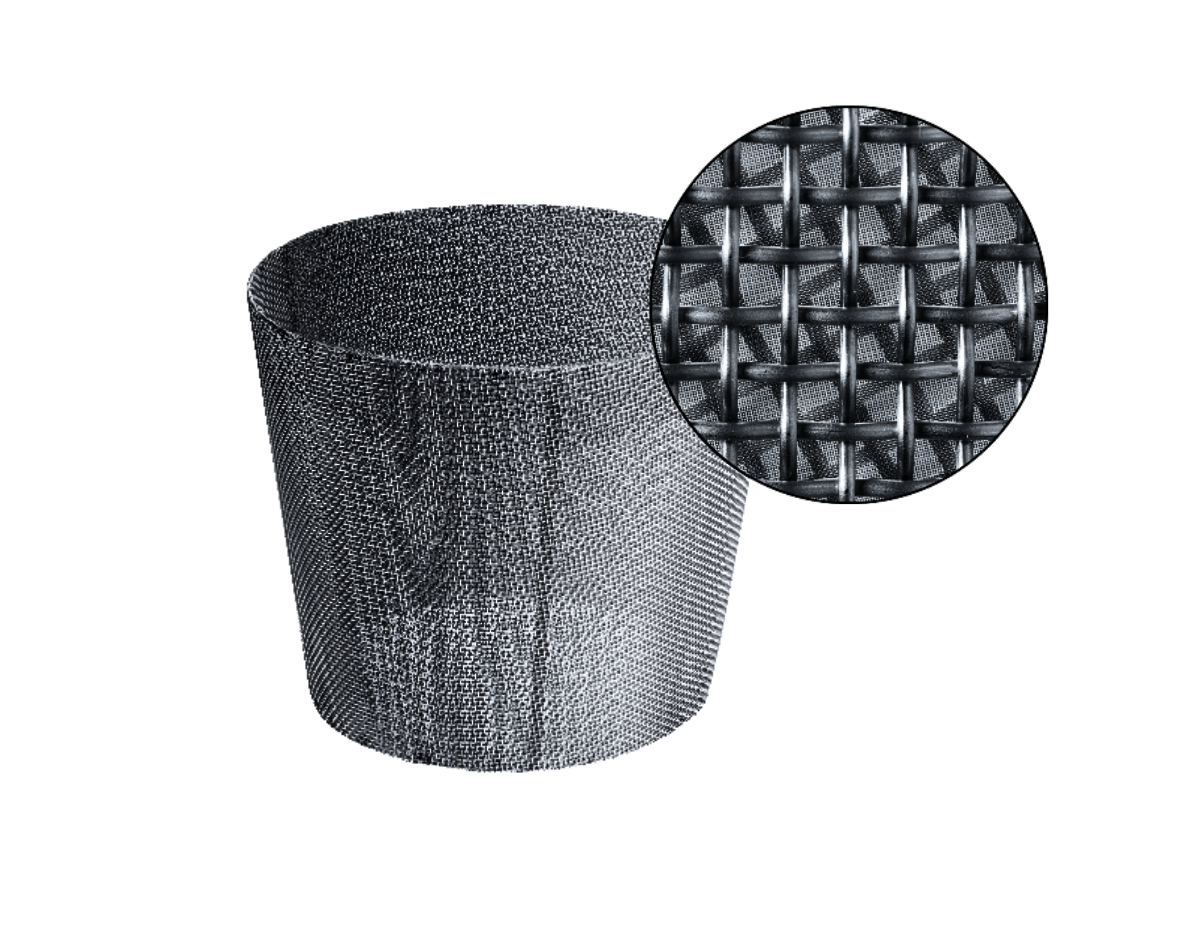
CONTACT
Are you interested in our product?
Then contact us via contact form, post@dds-filter.com or +49 271 401 4123.
We look forward to your inquiry!